Синтетическая нефть. Продукты перегонки.
Синтетическая нефть полученная из отходов, подвергается идентичной атмосферной перегоне с получением подобных продуктов (газ, бензин, дизель, мазут). Под вакуумом можно получить высококачественные масла.
В синтетической нефти из пластика, содержание серы меньше, чем в добываемой.
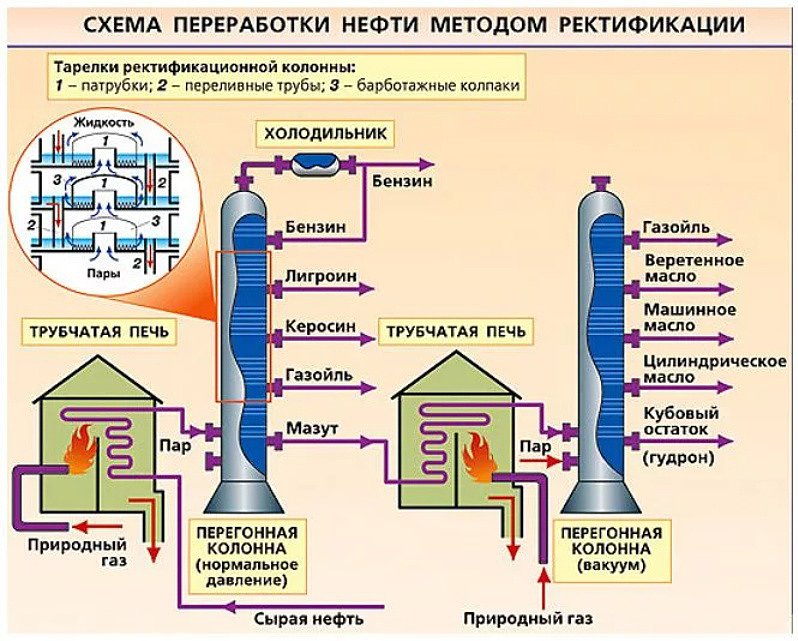