Изготовление пиролизной установки
Все железные заготовки для пиролизной установки вырезаны на лазере.
После высокоточной обработки, будет легко и удобно сваривать, монтировать детали.
Уже совсем близок тот день, когда приедут заказчики смотреть на работу установки со всей России.
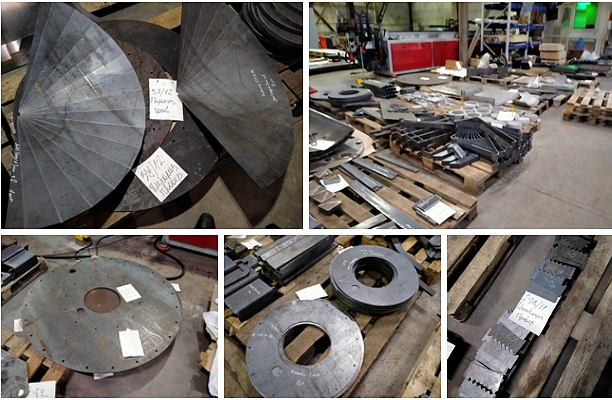
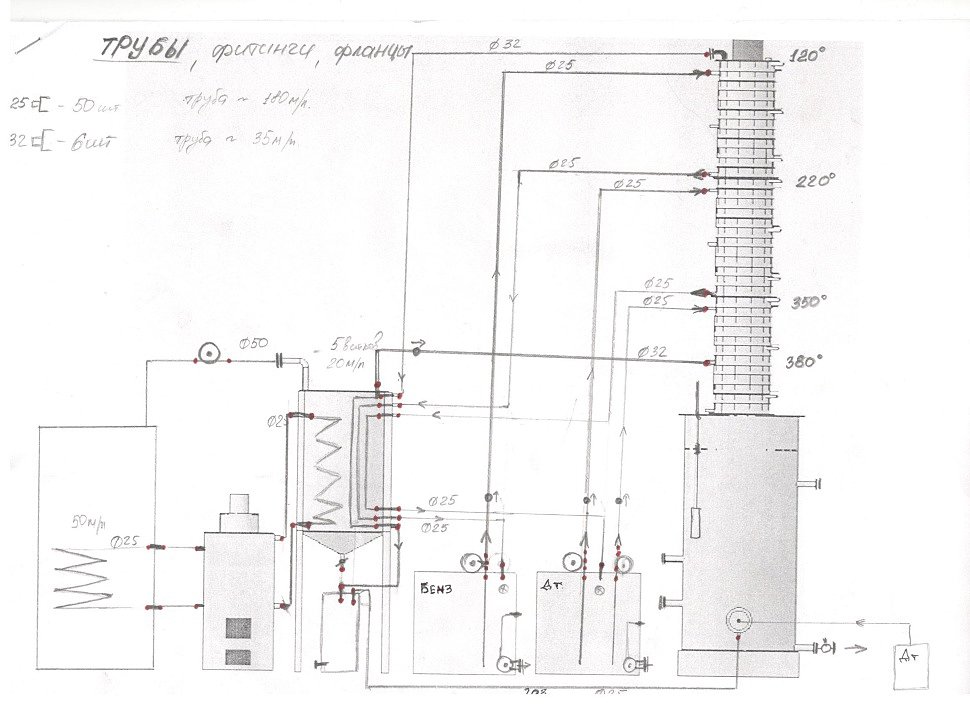
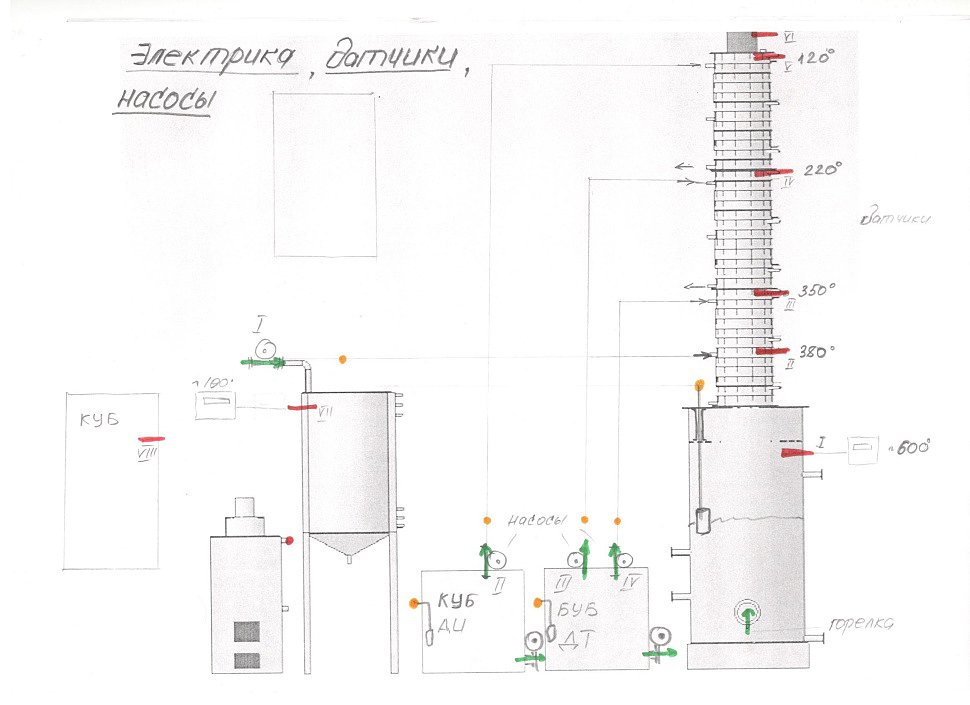
Пиролизная установка "Пантера" утилизация нефтешламов и отработанных масел