Кирпич для кладки барбекю
Заказчик захотел видеть свою печь в белом кирпиче.
Выбор пал на Кирово-Чепецкий кирпич.
Лотос м-300, 80 рублей за штуку.
Достойный выбор.
Скоро будем складывать красивую барбекюшницу в беседке.
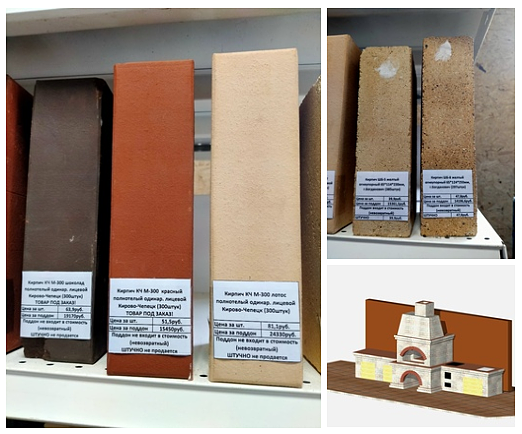
Заказчик захотел видеть свою печь в белом кирпиче.
Выбор пал на Кирово-Чепецкий кирпич.
Лотос м-300, 80 рублей за штуку.
Достойный выбор.
Скоро будем складывать красивую барбекюшницу в беседке.
Теги:
Всё отопительные, банные печи из кирпича в процессе эксплуатации начинают трескаться.
Чтобы сдержать этот процесс, делаем стяжной металлический каркас из уголка.
Русская печь с камином растет и долго прослужит своим хозяевам без текущего ремонта.
Пришло время осваивать ручной труд и рабочую специальность. Заработать на смартфон не плохой мотив.
Первый, самостоятельный, командировочный, трудовой выход сына на рабочие поля в 13 лет.
Начальный уровень - ученик ПОДСОБНИКа.
Теги:
Возникла нужда в плитке до 3 кВт. Пройдясь по магазинам, понял, что больше 1,5 кВт заводские плитки не делают.
Собрал из того, что было в гараже.
Стоимость затрат 150 рублей.
Теги:
Поступил заказ на интересную русскую печь с камином.
Нарисовал проект заказчику и уже чешутся руки.
Это будет красивая печь из желтого, колотого кирпича.
Закончена печь барбекю под облицовку.
Три дня работы и все довольны.
Дымоходы из 300 сэндвича уже были смонтированы.
Мангал, казан, тандыр.
Теги:
Уважаемые печники, все кто занимается интересным ремеслом по всей России.
Размещу ваше объявление на своем сайте. (бесплатно)
У вас будет своя оформленная информационная страничка, которая поможет клиентам найти вас через поисковики (Яндекс и Гугл) в вашем городе.
Разместим вашу фотогалерею на сайте.
Смотрите как это выглядит в готовом каталоге.
Отправляйте ваши объявления в сообщения группы.
Буду рад помочь вам.
Теги:
Установлена 6 метровая реторта в каркас. Ловким движением крана и 2 тонная труба легла на свое место.
Впереди ещё много работы, собираются все основные узлы пиролизной установки.
Теги:
Для измельчения отходов пластика и резины нужен шредер. Мелкая фракция лучше перерабатывается в пиролизной установке.
Купили мощный редуктор, который будет измельчать сырье.
Совсем скоро пиролизная установка "Барс" заступит на свою службу.
Теги:
Монтажные работы по сборке пиролизной установки идут полным ходом.
Вес конструкции более 8 тонн.
Совсем скоро начнем перерабатывать пластик и резину в топливо.
Теги: