Как найти денег для изготовления пиролизной установки
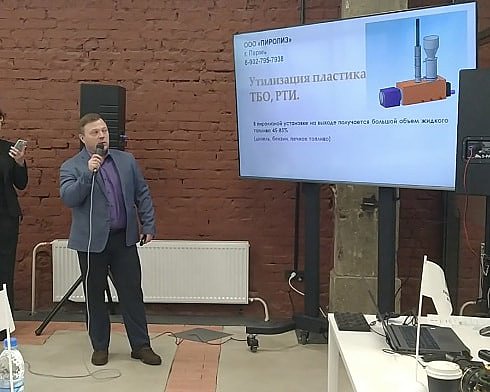
Прошел очередной стартап марафон "Разведка боем", на котором, я презентовал установку по переработке пластика в дизель. Мне очень понравился формат и подготовка к мероприятию. Инвесторы до начала всех презентаций были хорошо осведомлены о всех проектах. Получил предложения и визитки от инвесторов ещё до своего выступления.
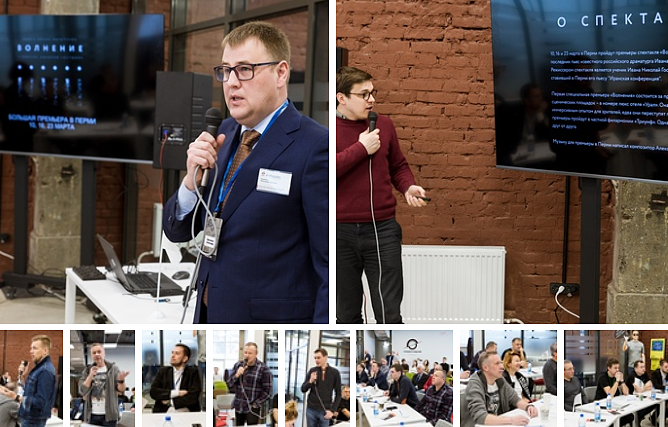
К нашему проекту был проявлен самый высокий интерес у инвесторов. Это вдохновляет нас на большие подвиги.